Pressure Sensor - Information
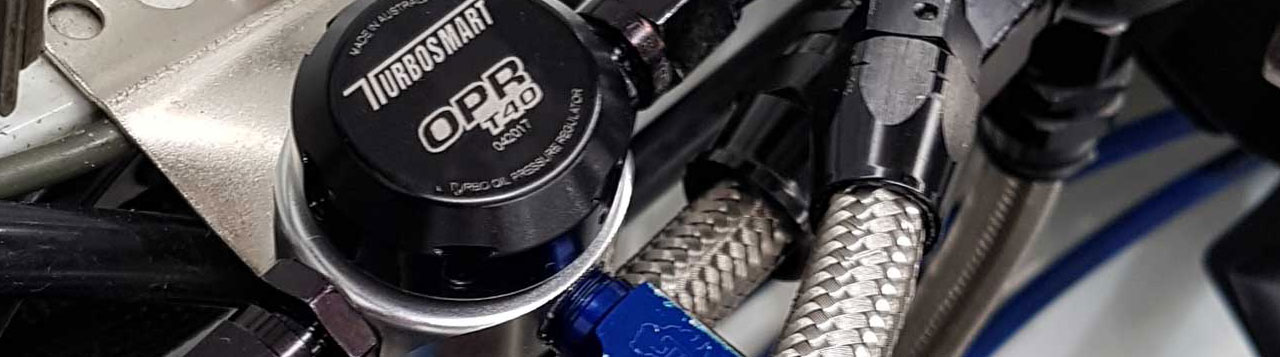
Here you will find information about pressure sensors.
The information is divided into sections as shown below.
- What does a pressure sensor do
- Different types
- Choosing a pressure sensor
- Connections
- Testing a pressure sensor
- Materials
- Installing a pressure sensor
- Accessories
- Problems with pressure sensors
- Compare pressure sensors
1 ▼
What Does a Pressure Sensor Do
- A pressure sensor is simply a sensor that measures pressure, such as oil pressure, air pressure, or fuel pressure.
- You use a pressure sensor to ensure that your engine is functioning properly and getting the right values to operate correctly, avoiding costly failures. You will get feedback on whether you have the correct oil pressure/fuel pressure and the right air pressure to provide optimal performance over time.
- To obtain the information from the sensor, you connect the sensor to the control system or alternatively to an analog gauge.
2 ▼
Different Types
Oil Pressure Sensor
Helps you measure the pressure in your engine or transmission. There are two variants: oil pressure switch and sensor.
- An oil pressure switch/warning switch provides an on/off signal.
- An oil pressure sensor measures the actual pressure.
A MAP sensor measures the air flow in your engine, for example, boost pressure. This is an important sensor to have when running turbocharged engines to avoid unwanted boost pressure, and it also indicates if you have lost boost pressure.
Fuel Pressure Sensor
Helps you monitor that you have the correct fuel pressure. This is extremely important to ensure that the engine receives the fuel it actually needs to provide the best possible performance and longevity.
3 ▼
Choosing a Pressure Sensor
When choosing a pressure sensor, it is important that it is suitable for the intended purpose. If you need an oil pressure sensor, it is crucial to review the technical specifications to ensure it fits your specific application.4 ▼
Connections
A pressure sensor typically has only one connector and one port where pressure readings are taken. Depending on the manufacturer and type of pressure sensor, both the connector and the port can vary significantly.
For example, Honeywell has a 3-pin ring connector with a 1/8" NPT thread at the sensor. However, this is just one of many variants available.
5 ▼
Testing a Pressure Sensor
If it turns out that the sensor does not provide a reading or gives a differing value, this is likely due to an issue in your application, leakage, or a misinstalled sensor, which can be causes of this.
Therefore, check that the installation has been done correctly and that the sensor is intended for the purpose.
- Check that the sensor is correctly connected to the control system or analog gauge.
- Ensure that you have installed the sensor for the correct application.
- Manually pressure test the sensor, and if you still receive no value despite the above points being correct, then the sensor is likely worn out. However, if you do get a value from the manual test, you probably have a leak or a broken/failing oil pump.
6 ▼
Materials
Depending on the quality and type of measurement range, a pressure sensor can be made from different materials. Some common types are:
- Stainless Steel
Most often used in higher-quality sensors designed to measure over 10 bar. - Brass
Cost-effective sensors that measure under approximately 15 bar. - Plastic
The simplest type of sensor that measures up to about 5 bar. However, sensors made of brass and stainless steel can also have the connector made of plastic.
7 ▼
Installing a Pressure Sensor
Make sure to install with the correct torque, which is determined for the specific application. Material and thread sealant can result in significantly different torque requirements from one application to another.Use appropriate tools (such as a wrench or socket) to install the sensor.
Ensure that the correct connector with sealing is used to connect the sensor. Incorrect or damaged seals/connectors can result in a short circuit in the sensor.
Make sure the sensor is installed with the sensing element facing downward. Any debris in the system can damage the sensor, and this minimizes the risk of that. Sensors mounted upwards can allow dirt to collect in the sensor, leading to damage or incorrect readings.
Do not install a pressure sensor directly on the engine block. Vibrations can damage the sensor.
8 ▼
Accessories
Weld ConnectionsThis allows you to easily install sensors on applications where you currently have no sensor. A simple solution like drilling a hole and threading it for a sensor works if the material allows.
Connectors
It is very important to have the correct connector for the right sensor. If the sensor is exposed to the elements, the connector should be weatherproof to avoid complications over time.
9 ▼
Problems with Pressure Sensors
Problems with sensors can occur in many ways, and to avoid this, we ask you to review our recommendations. Examples of reasons for a faulty/broken sensor are listed below.- Strong vibrations (misinstalled or improperly placed)
An oil pressure sensor usually does not have a design that can withstand vibrations, especially not a certain type of vibration emitted by some engines. Therefore, it is always recommended that pressure sensors not be mounted directly on the engine. Mount them on a hose that leads to the engine to mitigate harmful vibrations for the sensor. - Misinstalled sensor with the sensing element angled incorrectly. (Dirt accumulates in the sensor)
Sensors should be mounted on the side or above the component. Especially MAP sensors are affected by installation and how clean the system is. Both oil and other debris affect the measurement value. - Incorrectly connected sensor. No signal or value received. (Check the wiring diagram)
- Incorrect connector. The sensor allows dirt and moisture into the connection (which can lead to a short circuit)
▼
▼
-
Engine management / Electric
- Engine control system: The various parts available
- Ignition System Information
- Install motor control
- Pressure sensor - Information
- Temperature sensor - Information
- Buttons - Switches - Information
- Connectors - Information
- Cooling fan car - Information
- Exhaust gas temperature sensor - EGT Sensor
- Lambda sensor - Wide band lambda
- Relay - Information
- Relay box - Fuse central
- CAN protocol - Canbus
- Ethanol sensor - Information
- Gauges and Dash
- Trigger sensor information
- Dimensioning of cable [and fuse size]
- Distributor Problems (And Solution)
- How does an Ignition Coil work?